Motivation
-
Separated flow past an airfoil is characterized by multiple natural frequencies associated with various instabilities.
-
Traditional separation control forces at a single frequency and often neglects the influence of actuator dynamics (resonance).
Questions & Objectives
-
Is the effectiveness of a control strategy related to the natural flow instabilities and/or interactions?
Objective 1: Identify and analyze the various global dynamics in a separated flow configuration
-
Can we detect and leverage natural instabilities to understand, model, and control separated flow in a more efficient and systematic manner?
Objective 2: Investigate the effectiveness and efficiency of targeting the instabilities in open-loop experiments
Objective 3: Apply observations to design and implement effective closed-loop control strategies
Challenges & Approach
1. Traditional experimental methods for detection of flow frequency content are limited
- Localized dynamic sensors (location sensitive)
- High-rate global measurements ($$$)
Approach: Use modal analysis methods amenable to experimental techniques to obtain low-order, global estimates
2. Characteristics of 2D flow separation on airfoils is highly dependent on angle of attack and surface curvature
Approach: A canonical flat plate model retains the essential separation characteristics, eliminates curvature effects, and is amenable to both simulations and experiments
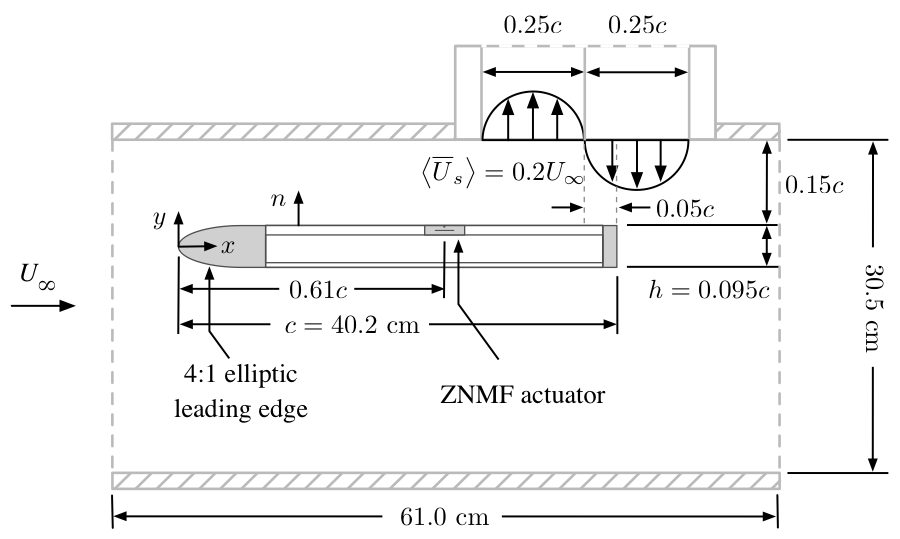
Experimental Objectives
1. Estimate global flow dynamics (time-resolved velocity fields)

2. Identify characteristic frequencies/instabilities

3. Perform open-loop control
Target characteristic frequencies by modulating actuator resonance. The extent and height of the time-averaged separation bubble is reduced during control.

Forcing at or near the natural shear layer frequency "feeds" the characteristic roll-up of the shear layer, which increases mixing between the high-momentum freestream and the low-momentum separated flow. This ultimately reattaches the flow further upstream with little control effort, or cost, described by the coefficient of momentum Cμ.

Conclusions
-
DMD extracts modal structures of the characteristic shear layer and wake components and results reveal interaction between the wake and separation bubble dynamics
-
Most efficient OL control scheme targets multiple flow instabilities rather than a single instability
-
CL control reattaches the flow (time average) by reducing the controlled shear layer oscillations